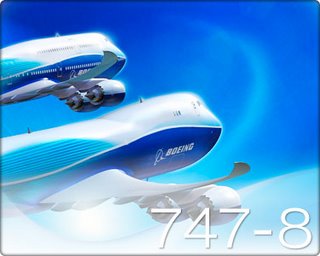
Let's first look at Information Management
and then its technology in one brush stroke.
Do you have any idea how large the Network Infrastructure is within the BCA (Boeing Commercial Airpalnes) division of Boeing? It use to be 58,000 nodes. I saw somewhere that it is now 128K.
http://www.boeing.com/news/frontiers/archive/2005/april/i_ids3.html
Now, this is just one out of several divisions that Boeing owns. Then there are the global partners. As my job as Infrastructure Manager for BCA, my groups included scientists, SA's, dBA's, technical SME's, Financial and Business Managers, Analysts and Chief and Fellow Architects, which represented the Network Infrastructure Services which I facilitated for all of Boeing's Commercial Airplanes division.
http://newsroom.cisco.com/dlls/2004/prod_071304.html?CMP=ILC-001

I wanted to go after them to do some business analyzing but I was thwarted by my good friend, the fellow architect, Craig Dupler. He was sure that the Network Operations Center, Large Lab, and Distributed Centers World-Wide was proactive. Because we were looking into these areas daily, I had no reason to dismiss his research. In fact, I later found that the NOC was indeed - way ahead of industry because of forethought and proactive processes.
http://www.northwestern.edu/observer/issues/2005/10/20/ford.html
Cost cutting was on the front burner; impose an Enterprise topology of WiFi, and look at SATCom as a potential backup service if needed. We has spinning globes up there to use, right? The offices and campus needed WiFi, but notably the greatest value for return on investment was within the factory walls. Compress this new technology and change out the way planes are manufactured by utilizing a 'moving line' using wireless tools. Savings? Big Time - Wireless' ROI 165% - Cost cutting of $2.2MM per yr. at an expenditure of just over $750K for implementation (hardware, security layered 128 bit over WAP / WEP). The moving line's ROI was into the several millions per plane and several more annually.
Then data stores; too much free space (white space) on servers hard drives. Take away the white space and use it for data. Cut down on the numerical number of servers; change out to more efficient hardware - less power consumptiom, etc.
Go to Microsoft to develop changes in their upcoming Long-Horn and have this consistency transfer to newer OS beta's that would benefit Boeing's way of doing business.
Other enterprise infrastructure demanded that all of Boeing's divisions deliver VOIP for telephony and video; inorder to adapt, Commercial Airplanes formed its own group to look into this Emerging technology; which I headed. My partner was a long-time Boeing employee and frankly, was a dead beat - Charles Green never offered to help me or steer me clear of unforeseen roadblocks or reefs that he surely knew were there. I took this virtual group of 50 active members on a fantastic ride - most of the technology that this group uncovered was implemented in one way or another. I was successful because of them. We produced tremendous effort and ROI for each technology implemented through project management and our ability to talk with each other as professionals.
Restructure not reengineer; A dismal failure was to re-engineer in the '80's and late 90's. But through examination, the internal and external processes the worker's used to service customer's, supply chain and partners were aligned for further cuts because of waste and needed mechnisms in place for delivering process improvements on a large scale. Process management and project management worked hand in hand; not withstanding ISO 20,000 for ITIL Library Framework or other series of ISO 90002 and Sigma Six (Black Belts) which were all designed for process improvments; ITIL Library Framework was a logical next step because existing processes were dumped into the framework and was used to streamline everything in IT. From portals to better servers, from our partners and supply chain - to inacting RFID for inventory; every thing was fair game to process manage.
Then partnerships were established in other countries for manufacturing airplane components like tails, and other parts - cutting off the supply which came from U.S. plants were now processes that went to global partners such as Russian Engineers and the plants their government set up to manufacture Boeing's parts. It was a vision that Mullaly and the Russian government had; without it - Russia would not purchase Boeing Airplanes. Many other countries had the same setup.
Finally, the final straw that broke the proverbial camel's back was the massive layoff's of over 55K to 65K skilled worker's. Wireless (WiFi) now campus wide, and in the factories was a large contributor to the worker's demise. So, the Machinist's Union worst fear materialized. There were several avenues to avert this catastrophy but that's another story.

Now, let me address briefly Ford Motor's tangled web of failure as an American citizen. In many parts of the country trucks are needed to do heavy tasks but that's not all. The majority of drivers thoughts and practices were never addressed by Ford. Ford took for granted the 'old' and mistakenly fragile adage, that if we build it, they will buy. Guess what - they were dead wrong.
Without substantial innovation like automatic steering control or traction control or for that matter better gas and diesel mileage with less emmisions, from their trucks and cars - global competition with these innovative ideas in place sucked the wind right out from under Ford.
Yes, the people base that Ford relied on as the 'dumb fucks', who will do anything we ask them too, did not respond to the new models, evident by the poor showing of financial profits, really gets to the heart of it all. Don't misjudge your clientel by treating them like they are dumb - even though, they maybe... treat them with respect and believe what they say and want and deliver it with creativity and innovative cost cutting ways.
Another point - the Union and Ford are so way outa touch - look at entry line level wages - $27.00 / hour. That's a joke - folks. Entry level - who do you think you are?
Ford! Is the business healthy? NO! So, do something about entry level wages. I'm not talking about skilled tool and die makers here, just the newbe, entry wage earner.
No comments:
Post a Comment